When you think about 3D printing, what do you picture? Cute little toys? Hobbyists? Printers with huge coils of plastic attached? If so, you’re a wee bit behind the times. 3D printing has come into its own, producing useful things rather than novelties.
Today, we have technology that can print everything from a 12 passenger bus, like Local Motors’ Olli, to a house. Doctors print prosthetics, human tissue and even bones.
But the big problem has been that, even though we can print all sorts of things, in many kinds of materials, it’s hard to do at production scale. 3D printing, also known as additive manufacturing (because you’re building up the item, layer by layer, rather than removing material to shape an object), is, to put it mildly, slow, and limited in the materials it can handle. It’s also extremely difficult to provide the consistent results and quality demanded in a production environment. In our mass-produced world, each part has to be identical; the variations we see in most 3D printing would totally mess up the assembly process.
HP Inc. and its partners are working to solve that problem, at least with plastics (others have already taken on the metals challenge). And they have plenty of incentive. There’s a US $12 trillion manufacturing market that is ripe for change.
Contract manufacturer, engineering and design firm Jabil, an HP partner (and supplier), says that four areas will be affected: exterior parts, interior/functional parts, manufacturing fixtures and PCB pallets. 3D spans all industries, with impact being felt in medical and dental (you can now have a tooth custom printed right in your dentist’s office), consumer electronics, automotive, aerospace, industrial and business machines, military, academic and more.
Jabil’s VP of digital manufacturing John Dulchinos said that many factors play in efforts to popularize 3D printing. For one thing, designing items for 3D printing is an unfamiliar exercise for most designers. They’re used to removing material to shape something, or squishing it through an injection mold, or pouring it into a mold. The notion that they have to build it up, layer by layer, takes some rejigging of thought processes.
It also gives much more scope to in part design. Some chunky parts can be considerably pared down without losing strength or functionality (which makes weight-conscious aerospace engineers very happy), and some parts that previously had to be assembled from several machined bits can be 3D printed in one piece.
Dulchinos says, however, that standardization and certification in the 3D printing world are still very much works in progress. Another challenge is scale. Manufacturers not only have to produce identical parts from one machine, they have to replicate them across multiple machines. Even slight variations can cause problems during assembly. Materials scientists also have some work to do, to produce materials with characteristics suitable for 3D printing.
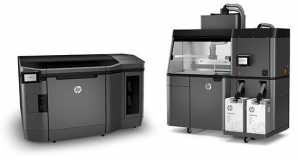
HP’s secret weapon in this endeavour is, oddly enough, the inkjet printer. The company’s PageWide technology, used in many of its business inkjet printers, moves the paper under a stationary print head that’s the width of the sheet. A PageWide head has 42,240 nozzles across its 8.575 inch print swath, and several can be snapped together to accommodate wider paper such as that in HP’s production presses.
That same head is used in the HP Multi Jet Fusion (MJF) 3D printers. But instead of spitting out coloured ink, the MJF head emits either a fusing agent or a detailing agent.
Here’s how it works, in broad strokes. The printer lays down a thin layer of a powdered plastic on its print bed. Then the bed passes under the head, where precisely drawn lines of the two agents create that layer of whatever is being printed. The detailing agent is used to define the edges, while the fusing agent takes care of the rest. Then a heater solidifies the printed area. Another layer of powder is laid down, the next layer printed and fused, and so on until the part or parts are finished.
Once the print run is complete, you have a bunch of 3D printed items inside a great mass of unfused powder. To dispense with that, an operator transfers the print bed (which is in a special trolley) to a second machine where the excess plastic is vacuumed out for reuse while a new trolley is rolled into the printer to begin another run. After the parts are cleaned up, there may or may not be additional finishing.
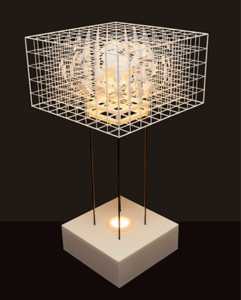
Because each item being printed is divided into thin layers in the pattern, all sorts of improbable things can be created. For example, if you saw a lattice ball inside another ball, you’d think the outer piece had been glued together after the little one was inserted. With 3D printing, the combination of agents, layer by tiny layer, produces output that is intact. That lack of adhesive actually makes the finished parts stronger.
Not everything is suitable for 3D printing, though. Extrusion molding is still more cost-effective for some high volume items. Funnily enough, though, Jabil has generated 3D printed parts for its extrusion molds.
HP even 3D prints its 3D printers, or at least, parts of them. Half of the custom plastic parts in Jet Fusion 3D printers are 3D printed.
Deloitte is confident enough in 3D printing’s potential to partner with HP to drive its adoption in manufacturing. “The digitalization of global manufacturing operations and practices will impact companies and consumers around the world, and 3D printing will play an important role in fundamentally changing manufacturing as we know it,” said Punit Renjen, Global CEO at Deloitte. “This alliance comprises two exceptional brands and brings together HP’s leading 3D printing platform with Deloitte’s digital manufacturing experience and global client reach.”
Deloitte plans to help organizations implement 3D printing technology, from HP and others, in their supply chain networks.
It may not be that difficult to sell. Jabil said that a year ago, it was actively pushing the idea of 3D printing to its customers, who hadn’t considered the notion. Today, Dulchinos said, “It’s just coming at us.”
There are certainly plenty of use cases. Johnson & Johnson, for example, showed off a surgical instrument, previously constructed in seven pieces, that was 3D printed as a single unit. That alone cuts manufacturing costs. An automotive assembly that was previously cast as a solid piece was reimagined as a lattice, using less material and eliminating weight, without compromising structural integrity. Other companies print gears, aircraft parts, and even sneakers. HP’s contributions are in the printing technology. It relies on partners to develop the materials to print with, which it then certifies for its printers.
One big gap that could hold back adoption of the technology is the lack of designers trained in creating 3D printed items. It’s a different mindset, needing different tools and software, as well as knowledge of a different set of material characteristics. It will help that the familiar Autodesk design software is part of HP’s 3D printing ecosystem, but there’s still going to be quite a learning curve.
Still, with companies like HP and GE building production equipment with 3D, Deloitte’s expertise, and the support of manufacturers like Jabil, 3D printing in manufacturing can only move forward.
I really enjoyed reading your article Lynn.
I agree with your statement that a huge problem in the development of this technology is the lack of designers trained in creating 3D printed items. I think 3D modeling is facing the same issue on a much smaller scale, besides many other problems it strives with.